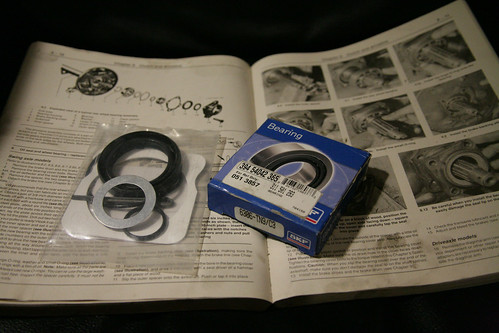
For the Volkswagen swing-arm rear axle, there are eighteen parts that must be assembled, in the correct sequence and in the correct location, to seal up the end of either the right or left side axle. Most of the parts are available for purchase in a Rear Axle Seal Kit. The eighteen parts needed are two spacers, an axle bearing, a washer, two "O" rings, a gasket, a seal, a bearing cover, the brake backing plate, four bolts and four lock-washers. If you have all the correct parts for the transaxle you are working on, it is a relatively easy project to do. If you are missing one of the parts, or one of the parts in not correct for that axle, or if you don't have a shop manual that shows the correct location and sequence for each of the parts, it is impossible to get the axle to seal. I now know, I believe, all the ways to do this project wrong.
The first thing I was missing was a proper shop manual, so I didn't know the exact order in which the parts needed to be installed, nor did I know the correct location for all of the parts. I thought I knew. I'd managed to get the rear axles of the Dune Buggy sealed up, so I thought I knew what I was doing. I didn't. I had most of it right, but, from the beginning, I was missing one key piece of information that resulted in my failure to get it right for the next six years. That's right, I've been driving this car with leaking rear axle seals for six years. Over that time, I've tried at least a dozen times to get it right and, until now, have always gotten it wrong. The problem has always been that I was certain that I knew the sequence and location for all the parts.
When you are sure you know something, you can't learn anything new about that subject. That is such an important concept that it ought to be made into a large banner and posted above every desk, every workbench, every mechanic's tool box, every kitchen, every bedroom, every library, every schoolroom, everywhere. If you think you know everything about the subject, you stop looking at that subject. You assume (always a dangerous thing to do), since you know what is going on with this area about which you know everything, that the problem has to be coming from something, or somewhere, else. I knew that I had the axle put together correctly, so the leak had to be caused by something else.
The problem was compounded by the fact that I was attaching Type III style brakes to the axle. This meant that the backing plate was different from what was originally installed on the car. That fact added just enough of a variable to blind me to the fact that I didn't actually know everything about putting together a rear axle.
What I know now is that when I first put the car together, I used all the right parts, but had installed one of the "O" rings in the wrong location. The way I did it made logical sense to me at the time, but in truth, was not logical at all. I was certain that I was doing it right, though, so when I discovered that I had a leak, I looked to other areas for the cause. I decided that if must be the bearing cover that was the problem, since that seemed to be where the leak was originating, so I got some different bearing covers and installed them. Big mistake. Major mistake. I thought that, since they looked pretty much the same with the exception of a drain hole at the bottom, the bearing covers where interchangeable. I was wrong about that.
If there is one lesson that I have had to learn over and over and over again throughout my life, it is that if you don't have a fundamental understanding of what you are doing, you are eventually going to run into trouble somehow. If you don't know how and why a system works, you'll never be able to solve the problems that occur when that system stops working. If you only know that this part goes there, but not what that part does in relation to the other parts to which it is attached, you'll be helpless when something goes wrong. You'll wind up doing what most people do when they have a problem, you'll attribute the source of the problem to the wrong cause. Once you've done that, you are on the road to frustration and despair. In the case of auto mechanics, you will replace part after part after part and never solve the problem, since you are attempting to fix something other than the actual thing that is broken. If you are like me, you can go down this road for six years before you finally discover that you don't know everything there is to know about a given subject.
The secret to problem solving is observation. It's not just a simple matter of looking at a thing. You have to look at that thing and actually see what is there. You can't look at it and decide that, because it looks like something similar, it is identical in form and function to that other thing. You have to look at the thing in relation to its surroundings. How does it fit? Where does it fit? If other parts need to fit on it or into it, will they? Look at the thing, not just for its similarities to other things with which you are familiar, but also for its differences from those other things. This sort of observation is a skill that if not constantly and consciously practiced and exercised will soon atrophy. You must work at your observation skills. They are the key element in your war against assumption. Don't assume. Observe. If you hone and polish your observation skills, you will find that they will serve you very well in all areas of your life.
After six years of 90 weight axle lubricant dripping all over my wheels and brake shoes, after a dozen or more attempts to fix the leak, after cleaning and replacing several sets of oil-soaked brake shoes, after giving up and resigning myself to never having rear brakes, I finally got fed up with the problem and decided to solve it once and for all. I finally got a proper shop manual and read it. Even then, I still got it wrong, so I read it again. Then I looked. I looked at the photos in the manual, and I looked at the parts on the car. I discovered two things. The first and most obvious was that I had been installing one of the "O" rings in the wrong place. The second was that the bearing cover that I had installed years ago as a attempt to solve the problem was the wrong part. The cover I had substituted for the original part was not holding the bearing in place, but was instead allowing the axle to move in and out about a eighth of an inch. It's no wonder that there were problems, I had made foolish mistakes due to my failure to observe.
What I did wrong was; first, to assume that I knew everything about assembling a Volkswagen rear axle; second, not to understand the fundamentals of the parts I was working with; and, third, not to look at what was there and see which parts were causing the problem. By assuming I knew what I was doing, I didn't allow myself observe or understand the problem. Once I finally looked at the problem and saw what was actually there, I was able to determine the cause, correct the mistake and fix the problem.
It is one thing to have a piece of data. It is quite another thing to actually apply that data to the real world. In my mind, this is the difference between the artist and everyone else. The artist knows the fundamentals of the medium in which he is working, be it painting, performing, sculpting, acting, programming computers, or fixing cars. The artist can see what is there in front of him/her, knows the fundamentals of how and why the thing works and can thus innovate, create and solve problems with an ease that seems like magic. When something goes wrong, the artist can look at the problem, know how things should be working, see where something went wrong, diagnose and solve the problem and achieve a smoothly functioning product. You can apply this viewpoint to every aspect of your life. I try to do this. I don't always succeed, but that doesn't keep me from continuing to work at it. Try it. Try living life as a artist. If nothing else, it's a lot of fun.
No comments:
Post a Comment